Primer on Spray Drying for Pharmaceutical Products
- Joseph Winslow
- Jun 13, 2020
- 2 min read

Spray drying is a method of producing a dry powder from a liquid or slurry by rapidly drying with a hot gas. This is the preferred method of drying of many thermally sensitive materials such as foods and pharmaceuticals. It has been around for many years with the first patents on the product dating back to the 1800’s.
In many cases spray drying can replace lyophilization as a way to control the particle size of the powder while dramatically decreasing the drying time. Many lyophilization cycles are measured in days, while the spray drying process can happen in minutes.
In practice, there are a few different designs for spray drying equipment, each with its own advantages and disadvantages as shown in the table here (courtesy of SDS Spray Drying Systems):
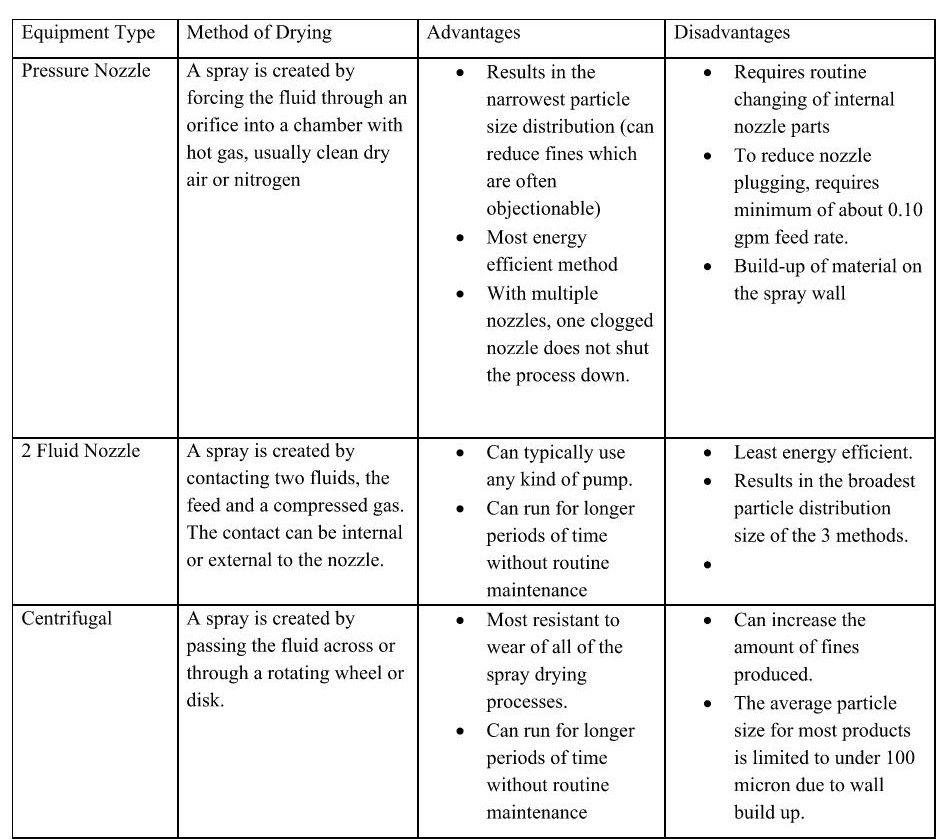
Spray drying provides several advantages over lyophilization or other methods of drying. The primary advantage as previously stated is the reduced drying time. In addition to that however, the parameters of the process can be adjusted to produce a specific particle size which can be important in subsequent steps of producing the final product. Also, spray drying can narrow the particle size distribution and reduce fines which are often objectionable. A fourth advantage is reproducibility. Once the process is developed and scaled up, it produces a very consistent product in a consistent time frame repeatedly. A spray dryer occupies a smaller footprint than a lyophilizer with equivalent drying capacity. Also, because it is a closed process, it might be possible to install the spray dryer in a room with lower ISO classification which equates to a lower capital cost overall.
Developing a spray drying process at a small scale can be tricky. The process works much better at a larger scale where the drying process has a bigger chamber to work in. Scientists must be careful to avoid false negative results when developing products at smaller scales. Other negatives include wall accumulation, higher maintenance costs, and clogged nozzles.
Direct compression oral solid dosage products can be produced from start to finish using spray drying in a matter of a few hours instead of a several days.
There are systems on the market whereby you introduce the product solution into the spray dryer, the product is dried and then transported directly into the tablet press, all without any operator intervention. This can happen in a completely closed process which is ideal for highly potent compounds to protect the operator from exposure to those compounds.
Obviously for those products that require the addition of lubricants or binders, additional steps are required prior to compression.
Spray drying is a process worth looking into for certain pharmaceutical products. There are several reputable equipment vendors with spray dryers on the market. These vendors can help you decide which method is best for your process.
Comments