The Building Blocks of Lab Design
- Joseph Winslow
- Dec 4, 2022
- 4 min read
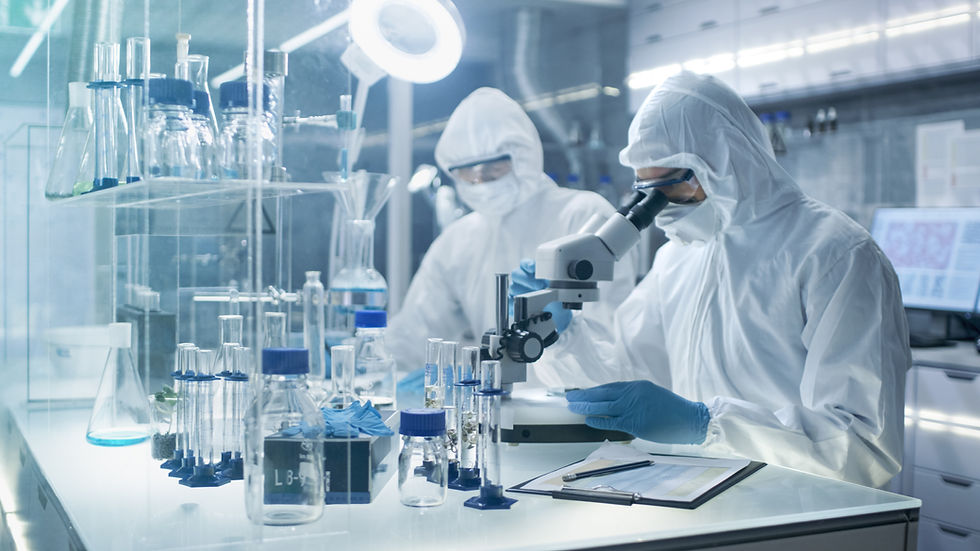
If you are in the Life Sciences industry in Colorado, California, Massachusetts, North Carolina or one of many other states, you are probably aware that converting vacant office buildings to laboratories is all the rage right now with developers. I wrote last month about some of the challenges of that construction https://www.jwconsultingengineers.com/post/converting-office-space-to-spec-lab-space
This month, I am going to talk about how design begins and what information the design team needs.
The process of gathering information for the design team is called programming. It entails understanding the basic functions of the lab (i.e. chemistry, biology, spectroscopy, etc.) which provide some basic information on what utilities and other infrastructure might be required. How many scientists are going to be working in the lab and an estimate on the required linear feet of bench space per scientist will also be needed.
Also, part of the initial programming and one of the most important tasks will be developing an equipment list. This list will include each major piece of equipment or instrumentation as well as all electrical, mechanical, plumbing services, or compressed gasses each may need. Let’s talk about each of these.
Electrical requirements may seem straightforward enough but are often not. To begin with, depending on the instrument vendor and where the equipment is manufactured electrical requirements may have different nomenclature standards. Some will be given in watts, while others provide volts and amps. Volts may be listed as 115V, 120V, 230V, 240V, 480V or a few others. Many manufacturers will not list the amps, but even if they do, they may list full load amps (FLA) or the required breaker size which mean very different things to the design engineer.
Further complicating the electrical discussion is the fact that some instruments come with their own Uninterruptible Power Supply (UPS) which could mean that separate components of an instrument all plug into the UPS (or not) and the design team just needs to provide power to the UPS (or not). And speaking of a UPS, the design team will need to know if the instrument needs a UPS, emergency back-up power (i.e. a generator), neither, or both. Another important item needed will be the plug type. The National Electrical Manufacturers Association (NEMA) assigns a standard number to the various types of plugs but finding that information from the manufacturer is sometimes a challenge. It should also be noted that not everyone in the world uses the NEMA standards.
Power to the laboratory benches is another consideration. Electrical engineers may specify power for the lab in terms of watts per square foot, or the number of circuits (not outlets) per bench. That is a key point. Scientists tend to know about how many standard plugs they need on a bench, but that does not equate to the number of circuits. A 120V circuit breaker is typically 20 amps, but each circuit can service several outlets. Be sure the scientists and engineers are speaking the same language when it comes to this point.
Mechanical ventilation is often needed for some laboratory instruments. But it can come in several flavors. Many chemistry labs are filled with fume hoods and the instruments needing ventilation are used inside the hood. Related to a fume hood, but very different in terms of design considerations are Bio-Safety Cabinets. Make sure you know which is most appropriate. Other instruments require a direct connection to an exhaust with a pipe or hose. Still others are situated on a bench near a snorkel.
Another column or columns in your equipment spreadsheet will be for plumbing, generally for vacuum, compressed air (including the quality required), compressed specialty gasses (Nitrogen, Carbon Dioxide, Argon, Helium and Hydrogen are some of the more popular), water, and drains. Flow rates are important to the plumbing engineer so he/she can design the appropriate pipe size. Total volumes are important to design the source of these utilities. Gasses can be provided in bottles, bulk tanks, or liquid dewars. Air and Nitrogen (and sometimes Helium) are often produced using a compressor which in turn will have its own utility requirements. The design team needs to know which source is most appropriate for your application. Vacuum can be centrally located and distributed throughout the lab or if the requirement is small, provided by a local vacuum pump.
One potentially complex question that may come up is water. To the uninitiated, water may seem simple, but the FDA recognizes 8 different types of purified water. I won’t get into the various types here (if you are interested, I wrote a blog post about it here: https://www.jwconsultingengineers.com/post/2018/08/16/8-types-of-water-recognized-by-the-fda), but knowing the purity required, flow rate, and total volume per unit of time is important to know and relay to the design team.
In addition to the equipment list, the list of chemicals that are expected to be used in the laboratory is important to the design team so they can design the appropriate storage, disposal, building code and safety requirements into the lab. The scientists may not know a complete list of chemicals, especially if it is a research lab. The science they do may lead them in some new direction creating a need for new chemicals. What is important to the National Fire Protection Association (NFPA) guidelines though is the class of chemicals and quantities of each that will be used or stored in the lab. Flammable, Combustible, Oxidizers, and Water reactive are just 4 of the 14 different categories defined by NFPA 400. So if knowing the exact chemical list is difficult, try to estimate the quantities of each classification.
Knowing and understanding most of the information above is more the purview of the engineer than the scientist, so it can be a daunting task to gather.If you are thinking of building a new lab or moving into a lab that will require modification though, the equipment list and chemical list are some of the first things the design team will ask for. Get them right and you have completed an important first step in your design.
Comments