HEPA Filters 101
- Joseph Winslow
- Apr 14, 2019
- 3 min read

If you’ve worked in the biopharma or medical device industry for very long, you have at least seen or heard of HEPA filters. HEPA is an abbreviation for high efficiency particulate air, originally called high-efficiency particulate absorber but also sometimes called high-efficiency particulate arresting or high-efficiency particulate arrestance. Whatever you call it, according to NIOSH (the US National Institute for Occupational Safety and Health), a true HEPA filter is one that can trap at least 99.97 percent of dust particles that are 0.3 microns in diameter. Just to give you an idea of how small that is, a human hair is about 50-150 microns. You will also see filters labeled HEPA that are rated at 99.99% and 99.997% efficient at 0.3 microns. ULPA (ultralow penetration air) filters can remove at least 99.999% of any airborne particles with a size of 100 nanometers or larger and are more commonly seen in the microelectronics industry.
HEPA filters work by trapping particles via three mechanisms, direct impact (just like it sounds), interception (glancing blow with filter fibers), and diffusion (random Brownian motion causing particles to collide and get pushed into the filter fibers).
HEPA filters are generally installed in one of 3 ways in biopharma and medical device cleanrooms. They are either installed in the HVAC unit or in the duct, are mounted in the ceiling and attached to a duct. In this type of installation, the air is pushed through by the HVAC unit. Lastly, they can be purchased and installed with an integrated fan to push the air. The latter are called Fan Filter Units (FFU). You will sometimes see HEPA filters installed in the return/exhaust duct, but this is the exception rather than the rule.
Here are some of the advantages and disadvantages of each.
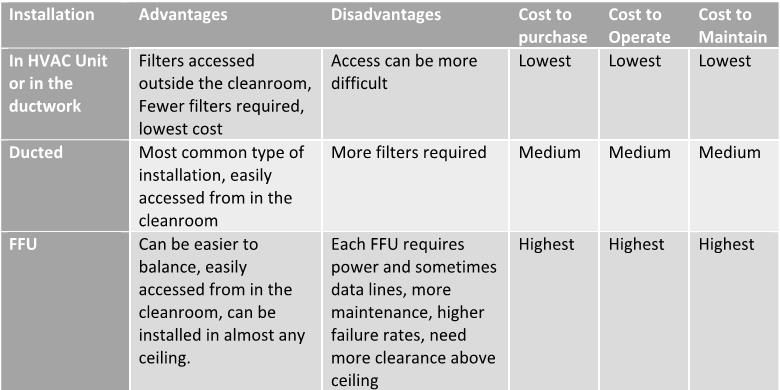
HEPA filters can be easily damaged, so should always be shipped and stored on their side rather than on their face. Additionally, only trained, qualified personnel should install the filters because not only are they easily damaged, but incorrectly installed filters are more likely to leak. For FFU’s and ducted HEPA’s that are in the room, they are generally installed after the filter housing (aka “can”) has been installed. The cheaper units come preassembled, but I would recommend against that because they can become damaged in shipment. Most have gel seals on the filter that is pressed up into a knife edge on the can. This needs to be done in an even manner so that the seal is made around the entire perimeter of the filter.
HEPA filters will arrive from the factory with a certificate showing that they were tested and had no leaks when they left the factory. This is important, but the filters MUST be tested again after installation to ensure they did not sustain any damage during shipping and installation. This testing is done by putting a known concentration of aerosolized Emery oil into the airstream upstream of the filter and then measuring that concentration at the face of the filter. ISO 14644-3:2005 provides test methods and criteria which I won’t go into here. These integrity tests are always done after the filters are installed and before the room is classified, and then again on a periodic basis. ISO 14644-2:2015 removed the requirement for testing every 6 months and replaced it with requiring a risk assessment to determine how often testing will take place. There is even mention that the 12 month retest period can be extended under certain circumstances.
Filter integrity testing (also called filter scanning, filter leak testing) is often done by an outside service provider, but bigger companies often invest in the equipment and training necessary for their own maintenance personnel to do the testing.
If a HEPA filter leaks, it is not the end of the world. FDA allows filter media to be patched if the patch is less than 3% of the total surface area or any single repair is less than 3 inches in length. Patching is normally done with silicone caulking. The filter media itself is only one source of potential leaks however. Other potential leak sources are:
Degraded gel seal or gasket
Filter media incorrectly installed in the can
Leaks in the can itself i.e. poor weld joints, leaks around tubing used for aerosol injection
Bolts/tabs that hold the filter media in the can, not tightened sufficiently
HEPA filters are vital to the proper operation and classification of cleanrooms, clean hoods, and other types of enclosures and are used extensively in the biopharma and medical device industries as well as the nuclear and microelectronic industries. It is important to learn at least the fundamentals of these filters if you work in these industries.
Filter manufacturers can be a great source of information on filters in general and their specific filters in particular. They are generally very accommodating and eager to help their customers learn how to purchase, test, and maintain these filters.
Comments